South Ayrshire modular homes on track for first tenants
A joint project to build the largest affordable modular housing development in Scotland is on track for first families to move into new homes by the end of the year.
The 63-home development, being delivered by Riverside Scotland and Connect Modular, part of The Wee House Group, was welcomed by South Ayrshire stakeholders during a recent visit to Connect Modular’s manufacturing facility and the development site.
The £9.8 million project is expected to be fully completed by Autumn 2022.
During the visit, Councillor Philip Saxton, housing and community wellbeing portfolio holder for South Ayrshire Council, said: “I’m delighted to see this important development of 63-homes well underway. This is the first affordable housing in South Ayrshire constructed using a modular build and I’m delighted to see this innovative approach that will deliver good quality homes for our tenants.
“Dundonald has lacked any development of social housing for decades and this is an important contribution to meeting housing needs not only in Dundonald but within South Ayrshire more widely. I look forward to completion and welcoming tenants into their new homes.”
The development will see a blend of house types, including one-bedroom flats, three-bedroom houses and two-bedroom amenity bungalows.
Riverside Scotland also confirmed recently that seven (11%) of the 63 homes are being allocated specifically to veteran households.
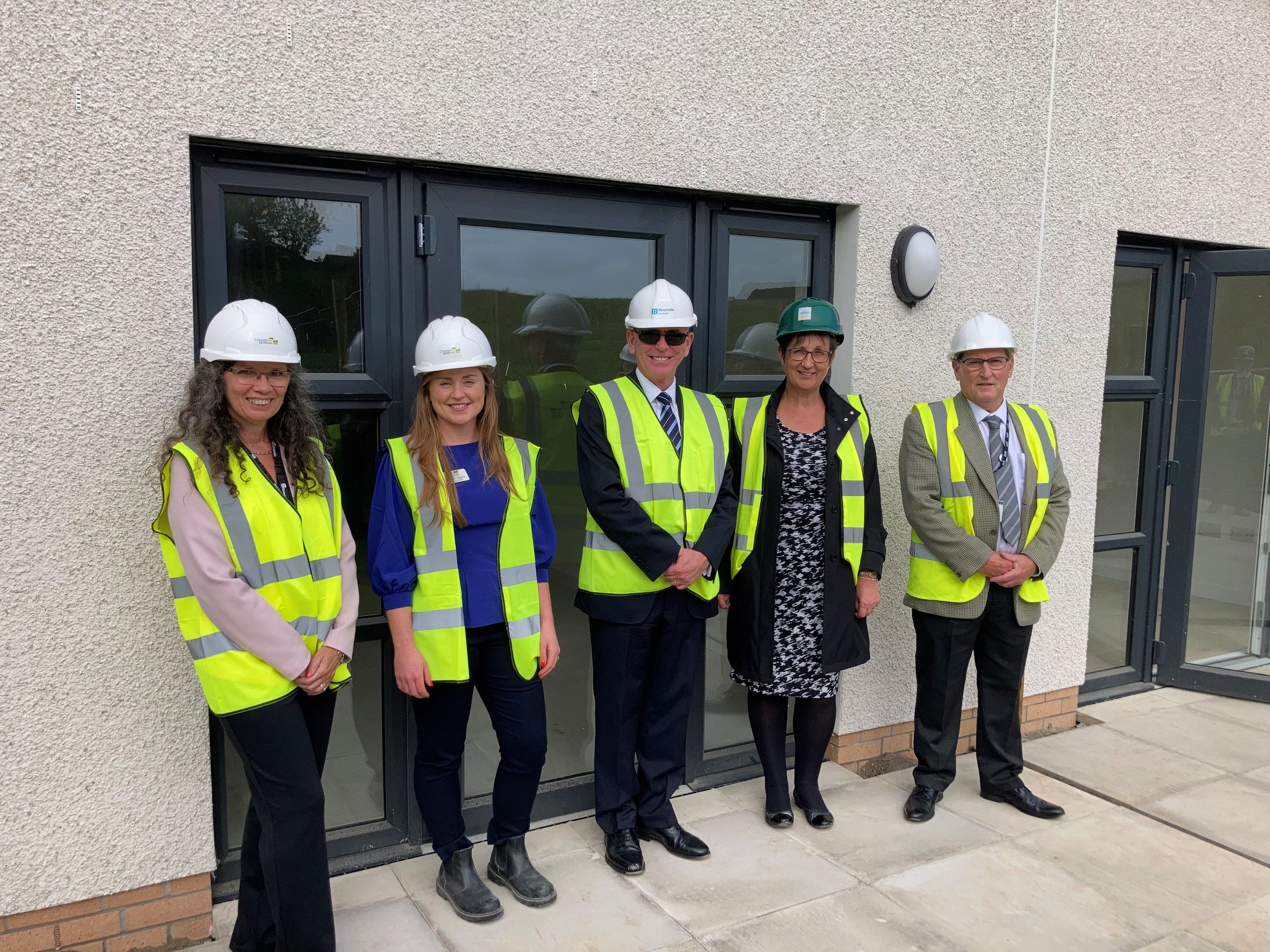
The project is Riverside Scotland’s first development in South Ayrshire, and will be an addition to its existing portfolio of 2,000 homes across North Ayrshire, East Ayrshire and Dumfries and Galloway.
Connect Modular, specialists in modular construction design and fabricate all houses in its Ayrshire factory. Houses are 90% complete when they depart the factory with kitchens, bathrooms, plumbing and electrics installed, facilitating a significantly shorter build programme and earlier occupancy. In comparison to a traditional build project, fabrication under factory conditions diminishes waste, improves quality, negates the impacts of adverse weather and allows for overlap of site preparation and build phases – a more efficient process all round.